Weighing instrument products
Packaging scale products
- Auger packing scale
- Gravity packing scale
- Belt scale
- Tons of packaging series
- Cumulative scale
- Special scale
- Valve scale
- Checkweigher
- Filling scale
- Pulse dust collector
- Feeding station
Palletizing products
Ingredient products
Pneumatic conveying products
Engineering products
Electronic control products
Non-standard products
CONTACT US
Wuxi Kefeng Automatic Control Equipment Co., Ltd.
Add: No. 11, Zhangshe Road, Hudai Industrial Park, Binhu District, Wuxi City
Business phone: +86-510-85874243
Palletizing Production Department
Contact: Chu Yushun
Tel: +86-13706193548
Stand-alone equipment department
Contact: Wu Dingguo
Tel: +86-15161509367
Weighing instrument department
Contact: Hu Yan
Tel: +86-13921158198
Ministry of Foreign Trade
Contact: Zou Dongsheng
Tel: +86-15190268138
Engineering, batching system and non-standard product department
Contact: Wu Haoqun
Tel: +8613606172914
E-mail: 8608415@qq.com
Automatic Batching Control System
Release date: 2019/4/23 15:30:57 Visits: 1360
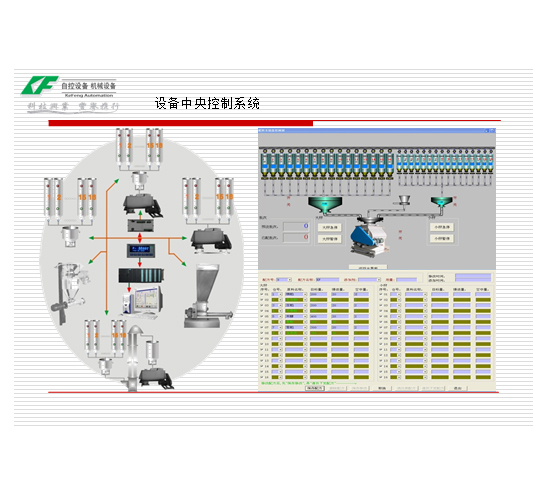
I. Systematic overview
This system is suitable for the transportation, metering and proportioning of powder and granular materials (such as refractories, cement, fly ash and pulverized coal, etc.). It is a complete set of automatic equipment for weighing and proportioning control, which uses weighing trolley, screw and belt as material conveying tools.
The electrical control part of the system is programmed and controlled by Siemens PLC according to customers''production requirements. According to the requirements of production process, the weight and flow of materials loaded into the weighing and batching truck are controlled by man-machine configuration monitoring system and PLC program, so as to achieve accurate metering and batching. As an automatic control device for dynamic continuous measurement and batching, the system can also provide accurate measurement data and control means for production control and management of various industrial sites.
The measurement accuracy of the system meets the standards of electronic hopper scale in the National Technical Supervision and verification regulations. In the production process, it can add materials into the weighing hopper according to the prescribed formula according to the fixed proportion weight value of various materials. When the displayed weighing value reaches the preset value (i.e. completing the weighing measurement of each kind of material), it can then unload the materials into the designated mixing equipment for mixing one time or several times in accordance with the unloading procedure to prepare for shaping or bulk packing. The computer automatic control system has the functions of automatic control of equipment and data management of weighing. It can record and print batching data.
Folding II. System Characteristics
The system can be applied to refractory, carbon, glass, ceramics, food, metallurgy, chemical industry and other industrial fields, and is suitable for the continuous measurement of materials and batching operations in the production process. Using this system can effectively improve the accuracy of ingredients, improve product quality, greatly reduce the labor intensity of workers, improve work efficiency and improve the working environment. It can basically achieve micro-dust in batching workshop and unmanned batching work, reduce production cost and management intensity of enterprises, and improve the technical level of production equipment and the scientific and technological content of products.
1. Flexible batching method, 2. Convenient remote monitoring 3. Simple on-site operation 4. Mature industrial application
Folding III. Design Principles
In the process of system design, equipment selection and implementation, the following principles are followed:
Mature technology: Mature control technology is the guarantee of the stable operation of the system. Practical verification of the control technology should be used as far as possible in the design.
Universality: Fully consider the convenience of equipment maintenance and spare parts purchase in the selection process, and select GE products as far as possible when meeting the design requirements.
Standardization: Standard methods are used in the selection of equipment manufacturer''s standard products.
Reliability: Increase anomaly detection as much as possible, system fault tolerance, improve system reliability, and shorten downtime to the minimum.
Expansibility: On the premise of meeting the requirements of production technology, expand the space (such as increasing the variety of ingredients, etc.).
Introduction of control system:
The batching control system is programmed and controlled by PLC according to the production process requirements of customers. Configuration monitoring system is used as the man-machine operation control interface to complete the control of various formula input and action commands. Through the man-machine configuration monitoring system and PLC program control, the material loaded into the weighing and batching truck is weighed and the flow rate is controlled, so as to achieve accurate metering and batching and improve efficiency.
Folding IV. Technical parameters
1. Microcomputer automatic control of the whole production process;
2. LCD can monitor the automatic working state of the equipment.
3. User operators can formulate, modify and edit production formulas.
4. Microcomputer can store many kinds of production formulas.
5. Electronic hopper scale adopts two-speed feeding control mode to ensure fast and accurate feeding.
6. Auto-parking alignment accuracy: +10mm;
7. The internal gauge, the height of the car body and the form of unloading outlet are shown in the drawings (which can be modified according to the user''s process).
8. Maximum weight of single hopper: 300-1500kg;
9. The feeding port of the electronic hopper scale of weighing truck is equipped with a sealing device and a dust removal system which can automatically lift and fall. It can effectively solve the problem of dust flying in the process of feeding and unloading, and make the production site environment clean and orderly.
10. Ambient temperature: weighing vehicle working site - 20 ~ + 50 (?) C, computer control room 0 (?) ~ + 30 (?)
11. Power supply: 380V + 10%, 50Hz, 11-37Kw,
The power supply of the control system is AC 220V + 10%, 50Hz, 0.5Kw.
12. Working mode: Microcomputer automatic operation, control room semi-automatic operation.